SOUTHEAST ASIA REPORT: VIETNAM, THAILAND, MALAYSIA
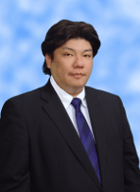
At the end of September, an auto parts manufacturer operating a plant near the southern Vietnamese city of Ho Chi Minh is struggling with a sharp drop in orders. The parts produced at this plant are delivered to Toyota group companies.
On Sept. 10, Toyota revised downward its production plan for the same month and October, adding about 70,000 units to the originally planned production cut of about 360,000 units in September, and cutting production by about 330,000 units in October.
The company also announced that it would revise its full-year production plan from 9.3 million units to 9 million units. Parts suppliers in Vietnam were affected by this. It was around the same time that Toyota announced its production cutbacks that the manufacturer mentioned above was told by its business partner that it wanted to significantly reduce orders for October.
In Vietnam, the number of people infected with COVID-19 increased rapidly from July 2021. In the suburbs of Ho Chi Minh City, where the number of infected people was particularly high, strict blockade measures were introduced. At manufacturing sites, employees were forbidden to move and were required to stay overnight to continue production. They brought cots and showers into the factories and managed to continue production. While they were working hard to maintain the supply chain in this way, they received a call from our business partner to cancel the order.
Toyota was not the only automaker to be forced to adjust production. On Sept. 17, Honda also announced that the production capacity utilization rate of its plants in Japan is expected to be about 40% of the initial plan for August and September, and only about 70% for early October. Subaru also announced on Sept. 17 that it would extend the suspension period of its domestic plants, which had been announced on Sept. 1 and Sept. 6. The finished vehicle plants of various companies in Southeast Asia are also being asked to make adjustments such as slowing down their production lines.
According to an auto parts manufacturer in Thailand, not only Toyota but also other manufacturers of finished vehicles were expecting that they would be forced to adjust their production in August and September, but that they would be able to recover in October. The impact of COVID on the supply chain in Southeast Asia was much greater than those involved had expected.
In Malaysia, a country with a high concentration of electronics-related factories, the spread of the outbreak has led to a blockade that has temporarily disrupted operations at the factories of major semiconductor companies, spurring a shortage of semiconductors.
Logistics dysfunction also plagues manufacturers. The spread of the new coronas has clogged container logistics, preventing Asian manufacturers from exporting their products as planned from mid-2020. If the U.S. stimulus package revitalizes logistics, the clog in container logistics from Southeast Asia to North America could continue. There has been a sharp increase in the number of customers wanting to rent warehouses in industrial parks in Thailand. This means that there is an increasing demand for a place to store auto parts inventory due to production adjustments.
Southeast Asia is being swept up in these massive and rapid changes in the market environment. While it is necessary to make the supply chain strong, it is unlikely that risks of this magnitude will occur frequently in future, and there will be a difference of opinion as to whether it is right to take measures to withstand such risks at great cost.
Source: Nikkei Business
PSR Analysis: Ho Chi Minh City has been locked down, Myanmar has been rocked by a coup, and the whole of Southeast Asia has been shaken up, mainly by COVID. According to the latest information, some countries and regions have eased restrictions, but looking at Southeast Asia as a whole, there is a great deal of uncertainty.
In many Southeast Asian countries, the automobile industry is an important industry that supports the nation’s manufacturing industry, and if orders from Japanese manufacturers cease, the survival of smaller parts suppliers will be in jeopardy. Many parts factories have been forced to suspend operations. The supply chain that has been built over many years of history is based on a strong foundation of trust, but when the foundation of our lives is shaken, they cannot live only on niceties.
Of course, the impact of COVID is huge, but the market will not be stable due to a combination of factors such as the shortage of semiconductors, increasing political instability, and the influence of US and Chinese policies.
I believe that the optimistic view that time will solve many things is dangerous. Whether it is COVID or semiconductors shortage, it is realistic to expect a prolonged period of time. The search for the best solution for the supply chain will continue. PSR
Akihiro Komuro is Research Analyst, Far East and Southeast Asia, for Power Systems Research